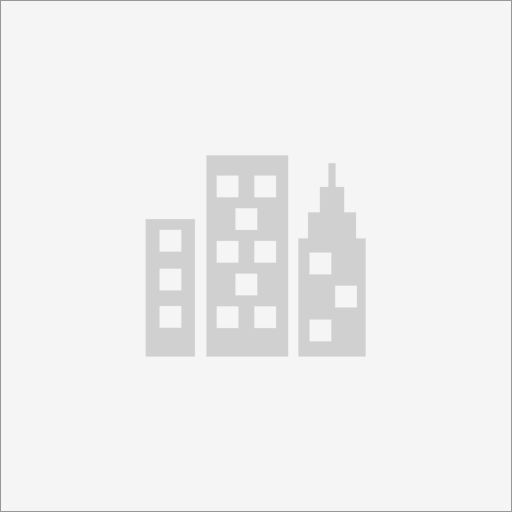
Aptar
nearmejobs.eu
JOB TITLE: Director Manufacturing, Pharma NA
LOCATION: Congers, NY
Improving Health through Science and Technology! At Aptar Pharma, we specialize in Drug Delivery offering Innovative Devices, Services and Solutions focused on the Patient Experience. Aptar Pharma is part of Aptar Group, a global leader of dispensing systems for the packaging industry. Aptar Pharma has been setting the standard in drug delivery for decades providing health technology solutions and services enabling effective patient treatment. Be You, Be Aptar!
Aptar Pharma has an exciting new opportunity at out Congers, NY facility for a Director of Manufacturing, reporting to the North America Pharma VP and GM.
Essential job responsibilities:
- Accountable for the daily, monthly, yearly production output all across Congers site
- Establishes systems to collect metrics, analyze productivity and set performance targets that will meet revenue and cost goals. Leads the development and deployment of manufacturing practices focused on quality and continuous improvement.
- Plan and Manage effectively the financial CAPEX and OPEX envelop
- Lead the strategy development and continuous improvement deployment for OpEx across the Pharma North America with short and long-term goals for improved performance, increased service levels, and reduced COGS, contributing to operational efficiency improvements and EHS performance exceeding Company Standards Industry standards and site goals.
- Ensures robust plant safety and security procedures and training are in place and that operations are in compliance with all required regulations.
- Close working relationships and consensus building are required with all other functional leaders, staff and key stakeholders
- Requires the ability to contribute as both a leader and individual contributor in supporting the business needs.
- Lead and inspire for a site Operational Excellence culture and mindset.
- Coach and train the OpEx structure as defined Operating System global operational excellence program
- Ensure OpEx and EHS are aligned for achievement of site level goals and continuous improvement driving “best in class” results.
- Lead and inspire an organization and a culture of compliance with GMP’s, SOP’s and procedures to ensure that the Food and Drug Administration (FDA) and ISO regulations and quality standards are met.
- Provide LEAN Six Sigma expert advice, support, coaching and mentoring to leaders and their teams for the execution of the Operational Excellence Strategy.
Required qualifications and skills:
- Bachelor degree in Business or Engineering. Engineering Degree, Post graduate degree highly desirable.
- 10+ years in a manufacturing environment or equivalent professional business experience.
- Experience in designing, developing and deploying Business Excellence/Continuous Process Improvement programs (Lean and Six Sigma). • Lean / 6 Sigma Certification, including Master Black Belt.
- Experience with the following methodologies and practices: FMEA, Kaizen, Lean tools, 5S, Visual Factory Aids, SMED concepts, VSM, VOC and Poke Yoke
- Experience in the Medical Device industry highly desirable
- Demonstrated track record of process improvement and cost savings success
- Solid understanding of Engineering, Project Management, Lean Principles, Six Sigma, Financial acumen.
- Demonstrated experience and ability to manage cross functionally with direct and indirect influence
- Proven experience and Ability to Coach and facilitate individually and at the large scale level across a diverse organization influencing all
- Advanced skills in statistical software packages
- OpEx/Lean Six Sigma/PMI certifications Skills/Competencies:
- Demonstrated track record of leading within complex organizations requiring strong influential communication skills • Effective decision-making skills and proven accountability for business results
- Ability to negotiate and balance decisions and priorities across needs across the Company with all stakeholders
- Experience in creating sustainable processes via data-driven iterative process improvement – with a high attention to detail, and organizational skills
- Exhibits a high level of energy and possesses excellent interpersonal skills
- Strong analytical/statistical problem-solving tools (DMAIC/PDCA/8 Disciplines) Ability to support multiple projects and balance priorities.
- Strong coaching, influencing, facilitation and organizational skills including and understanding of and proficiency in Change Management.
- Self-starter with experience effectively navigating high levels of ambiguity and complexity
- Ability to work cooperatively at all levels in matrix environment to build and maintain positive relationships required to accomplish organizational goals • Excellent communication skills and interpersonal/team effectiveness- ability to succinctly and accurately communicate to various levels of employees
- Strong attention to detail, analytical, planning, organization and time management skills to effectively execute project plans and budgets
- Computer literacy including Minitab, Visio, Smart Sheet, PowerBI, Asana, Microsoft Office Suite, and Microsoft Project.
PHYSICAL REQUIREMENTS
Exerting up to 20 pounds of force occasionally, and/or up to 10 pounds of force frequently, and/or lift, carry, push, pull, or move objects.
- Heavy work: Exerting up to 100 pounds of force occasionally, and/or up to 50pounds of force frequently, and/or up to 20 pounds of force constantly to move objects. VISUAL ACUITY The worker is required to have close visual acuity to perform an activity such as; preparing and analyzing date and figures; transcribing; viewing a computer terminal; extensive reading; visual inspection involving small defects, small parts and or operation of machines including measurement devices and/or assembly or fabrication of parts at distance close to the eyes.
WORK CONDITIONS The worker is subject to inside environmental conditions: protection from weather conditions but not necessarily from temperature change. The worker is subject to noise: There is sufficient noise to cause a worker to shout in order to be heard above ambient noise level.
Apply
To help us track our recruitment effort, please indicate in your cover/motivation letter where (nearmejobs.eu) you saw this job posting.